This project is featured as part of the D5 Digital Design Week: AI & Sustainability. To learn more, click here.
Many children experience chronic heel discomfort, particularly between the ages of 6 and 16, when 55% develop Sever’s disease. This painful condition affects the heel, causing it to lose its flexibility and radiating pain that can extend to the calf and thigh. It can make walking, standing, and performing everyday movements difficult in severe cases. Current treatments, such as corrective straps and professional rehabilitation, can limit a child’s mobility for months, and if left untreated, the condition may persist into adulthood.
Despite its prevalence, this issue has often been overlooked, much like how many of us remember struggling to find the perfect pair of shoes while our feet were still growing. Children’s feet, with their small bones and soft tendons, require shoes that offer targeted support and room for growth, yet finding that balance has remained challenging.
Function-Oriented Design Ideation
3D Print-knit is a new material that combines the wisdom of traditional textiles and the power of 3D printing.
After studying children’s foot health issues and potential causes, Yumeng Li & Zongheng Sun of PEAR & MULBERRY learned that suitable shoes should have flexible soles that bend with every step, offer support in the center of the shoe to eliminate twisting and give shock absorption and stabilization in the heels. Also, the flexible upper helps prevent joint injuries and fatigue. These criteria triggered the design process and were transferred to the key elements of the We| aver+.
Fig.2
Rather than drawing inspiration from the softness of textiles, the solution was found in the structural properties of hollow-loose knitting. This technique, resembling chainmail, is made from the same material but offers varying stretches and support in different directions. By 3D printing this structure with elastic TPU, the shoe’s upper wraps tightly around the foot while providing flexible space for the foot to fit comfortably.
Fig.3
Computation-Optimized Design Experiment
Customization is no longer costly but necessarily accessible.
To achieve the perfect balance of flexibility and stability for different foot conditions, the team used 3D scanning to capture the accurate geometry of children’s feet. The scanning takes only 2 minutes and is then transferred into the 3D models that can be used for foot pressure simulation. A heatmap was generated from the simulated pressure distribution and exported as one of the design inputs. Based on one heatmap, exhaustive design combinations can be created to provide options for fine-tuning the element thickness and orientation of print-knit forms. Using plug-ins like Kangaroo, Weaverbird, Mesh+, and LunchBox in Grasshopper, the DOE optimization of forms can be done rapidly on 3D models to satisfy customization requirements.
Fig.4 3D Scanning creates digitalized foot mockup with high fidelity
Fig.5 Dynamic Soles are computationally designed based on data diagnosed from foot pressure mapping.
We | aver+: A plus is brand new
We | aver+ is a revolutionary step in both 3D printing and foot care service, which brings the benefits together as listed below
Knitting + 3D Printing
We | aver+ is the first therapeutic children’s shoe system specially designed for children aged 8 to 14. It learns and amplifies the microstructure and mechanism of knitting in fabric to build with a single material by 3D printing with pretension: It is stretchable in one direction while stable in the perpendicular direction to ensure the shoes have the flexibility for movement and enough support for protecting growing bones.
Fig.6 Print-knit TM reinvents knitting with 3D printing technology
DM + AM
The pressure digital mapping (DM) is transferred through parametric design to achieve a scientific distribution of support and elasticity across the entire structure with anisotropic zonings precisely customized for the more frequently changing foot conditions. The integrated additive manufacturing (AM) system realizes the vision of customized care at a lower cost and with fewer carbon footprints to demonstrate the vast potential of customized, sustainable, and healthier children’s shoes.>50% Recyclable TPU is adopted to enable more sustainable reproduction for rapidly developing children’s feet with lower costs and fewer carbon footprints.
Based on data diagnosed from foot pressure mapping and 3D scanning, optimized with computational design, We|aver+ shoes can furnish support-comfort balanced solutions to fit diverse foot conditions without hindering normal foot growth.
Fig.7 Process of rapid 3d printed prototyping and visual forms.
Enumeration + Customization
Computational design methods not only exhaustively generate design options but also outfit the finetuning of local configurations of the element thickness, porosity, and orientation to customize the functional properties of the shoe printed in one piece with one material. The print-knit upper performs directional stiffness, boosts ankle-wearing comfort, and eliminates the use of shoelaces. The dynamic sole customizes zoning softness to relieve Calcaneal Apophysitis pain on point.
Fig.8 Exhaustive design explorations through generative computing
Components: Four functional parts printed all-in-one
The ankle cushion delivers a soft touch to the ankle and enables slip-on function without shoelaces.
Fig.9 Components
Featuring anatomical arch support, the modular insole cradles the foot and customizes zoning softness to relieve Calcaneal Apophysitis pain with enhanced comfort from heel to toe.
Fig.10 Customized zoning softness
The print-knit upper is calculated with parametric tools to be functionally heterogeneous but simple. Made from 3D-printed fabric with anisotropy, it wraps tightly around the foot in one direction to maintain stability yet is flexible in another to give the foot enough flexibility.
Fig.11 Print-knit upper
The dynamic sole contributes to comfort with pre-designed zones. The sole is easier to bend at the toe part for better toe space. At the heel part, the structure produces responsive foot pressure distribution. Moreover, wrong gait and foot pathologies could be observed and diagnosed accurately from the wear of the parametric bottom grid.
Fig.12 Dynamic sole
We| aver+ care for growing pains, outfitting customized support to eliminate foot pain and worries and add styles, mobility, and happiness.
Future Opportunities
– By combining parametric computation and digital fabrication, We| aver+ illustrate the huge potential and infinite possibility of customized, sustainable, and healthier children’s shoes.
Fig.14
– The fabrication process becomes efficient with the help of 3D printers. TPU is lightweight, water-proof, and as soft as fiber, and it will automatically maintain its shape once printed. Moreover, this material is 100% recyclable, which enables reproduction for more frequently changing foot conditions. The price of 3D printing TPU has dramatically dropped, and it only costs $5 to print a pair of shoes. The printing time depends on the structure design, usually 8-14 hours.
– The project started in January 2020 in Cambridge, Massachusetts, USA. The fabrication process was conducted with the help of FabLab at Harvard GSD. We will continue to work on simplifying the scanning, calculation, and generation process to improve the clinical application of implementing We|aver+ systems in the near future. We are actively reaching out to 3D printing startups in the Boston area to integrate biodegradable and durable cutting-edge formulations to enable this project on a higher sustainable level.
“Everyone grows from a child into an adult step by step. We ensure that every step of the child can be healthier and happier through AI-enhanced technology, and humanity-centered design.”
Image credit: Courtesy of the designer.
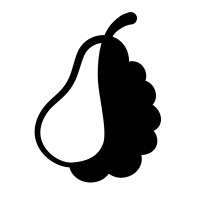
PEAR & MULBERRY is a design technology brand that manifests concepts for chicer and healthier lifestyles by advancing multi-sensory interaction and computational design. PEAR & MULBERRY facilities design research under two design groups: Para Plays – “PEAR” Augmented technology that blurs the reality with the digital universe, creating an ultimate play experience. Soft Matters – “MULBERRY” Why not make it softer? Flexible, sustainable materials are integrated seamlessly with enhanced ergonomic compatibility.
Contact:
Designers: Yumeng Li & Zongheng Sun of PEAR & MULBERRY